Conveniently, during a recent round of skipping, I had retrieved the following three panel-glazed french doors - how handy!
These could be made to fit into the remaining gap in the end wall of the shed, but first the opening needed to be made. The gap that was formed between new and old rooves was slightly too high, so some boards needed to be removed to lower this. Sawing off parts of your shed is slightly weird, but strangely compelling.
To fit in the open spans between uprights, the french doors needed to be cut into parts. Some care and tightly sealed eye goggles were needed in case the blades hit glass
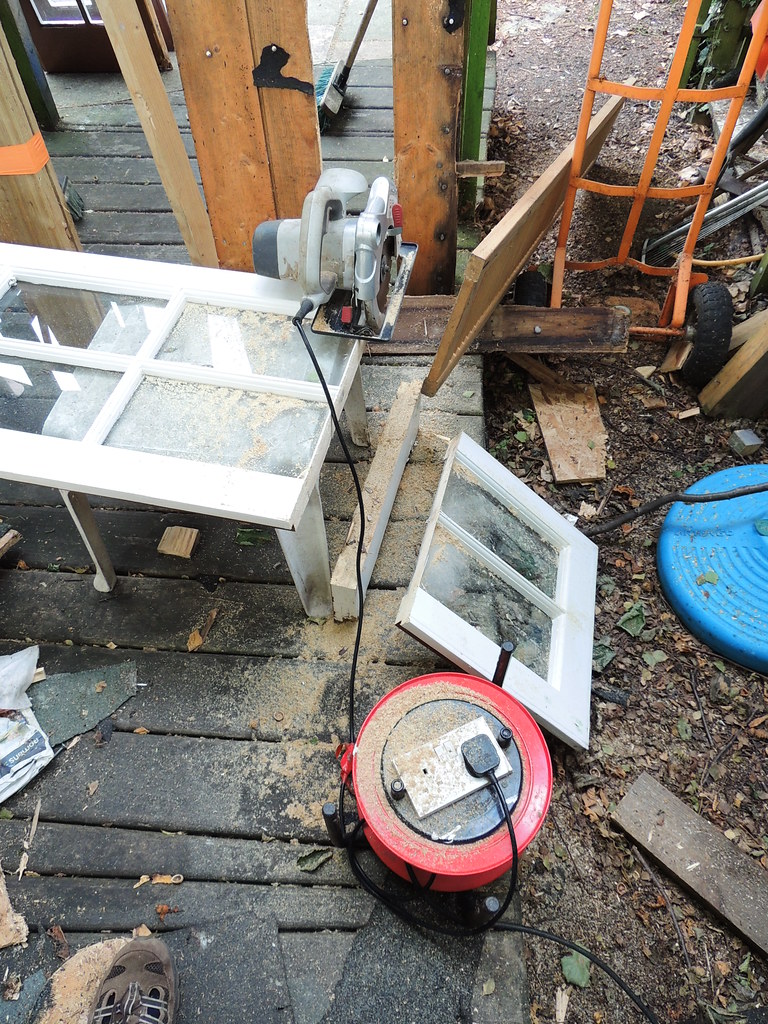
Here's the first panel in situ
Fitting in the next one and so on. Naturally this involved climbing up old shelving - you get the idea
*INTERLUDE* Here's a frog I found outside whilst positioning a ladder *INTERLUDE*
Eventually it looked like this
The gaps left were panelled over with leftovers from the wall section removed earlier...
Once completed, the windows were masked ready for painting
After painting it looked pretty nifty...
And inside, in the evening, it has a cathedral vibe going on. I might stain the windows!