The processes involved when I make stuff: sculpting, programming, electronics, carving, moulding, etc. Mostly puppets, automata, sculpture, occasionally furniture, interactives, food, etc. Usually fairly detailed and image-led. Please reuse any ideas, tips, thoughts and approaches.
Saturday, 31 March 2012
Friday, 30 March 2012
Hinged metal maggots
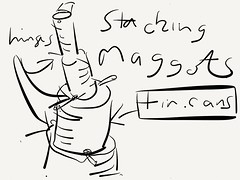
Hinged metal maggots
Originally uploaded by rosemarybeetle
Made with Paper
This is a small scale version of an animatronic maggot, based on a human sized one I saw at a festival in Arnhem once. That freaked and groaned impressively as it ground round, powered by a washing machine motor
Tuesday, 27 March 2012
Making an Arduino power supply cable look wooden


With nice wooden plugs an ugly black plastic lead is not really what anyone wants!
The black lead on the left was revamped into the lead on the right by sawdust coating it using latex as a flexible bonding agent.
Latex and sawdust forms a composite material which is much physically robust than either on their own. The latex provides flexibility and the dust gives bulk and resilience.

Liquid latex from an art supply shop was used, without any thickener adding. It uses ammonia as a suspension fluid which does smell rather strongly. Use in a ventilated space!

Latex was poured into a shallow container

Sawdust was sifted to get a fine powder.

The sawdust was dusted over the wet latex.

This was left to dry, then the process was repeated.

Eventually after three coats it ended up looking rather tasty and root-like!

A close-up of the joint with the mains plug.

Here is the head complete with swanky new cable.
Thursday, 8 March 2012
Adding wooden plugs to the power unit


Here it is being held temporarily in the vice, while a cramp is attached.

A conical casing for the %v end of the power lead had been turned, which had also cracked. This turned out to be helpful, as it was the easiest way to fit the plug

A pair of locking grips was used as a cramp to hold it while the glue set.

Once glued and cramped, they were let to dry


Here is the business end of the finished mains end of the plug.
The transformer is held in place firmly using hot glue

And finally the finished end of the 5v plug
Saturday, 3 March 2012
Creating a new oak casing for the new power unit

The second stopped working after it was encased in oak. It was not obviously damaged externally. It is likely it was broken inside by vibrations from the sander, as the plug was in situ, when it was subjected to some serious RPM.
See below for the steps undertaken to create this...

A new casing in the vice, being routed out to fit the plug.
Note the guide rail cramped to the bench. This is a guide for the handheld router to keep to a reasonably straight edge

A close-up of the inside of the casing, partly routed.

Fitting the plug to test the depth

The casing with routing completed, prior to finishing.

Checking the plug fits with both halves of the casing in place.
As the last unit was killed by vibrations, this one was to be finished without the unit in it though

To do this, the two halves of the casing needed to be sanded whilst kept aligned. The plug had done this in the previous attempt, but was not in place in this version.
Tow screws were inserted in one half of the casing to create guide pins to keep the halves aligned whilst sanding.

The guide pin after the screw head has been removed. This is to fit into a hole in the other half of the casing. (there are two of these)

To mark the other half of the casing, the two halves were aligned, then pressure applied in the vice.

This created an indentation, to mark where the alignment hole needed to be drilled.

The completed halves.

The completed casing, ready to be finished

The finished casing after planing and sanding. Unfortunately it cracked when the router bit in a bit too strongly. This cracked was later glued back together